What are the benefits of using lightweight materials in electric vehicle construction?
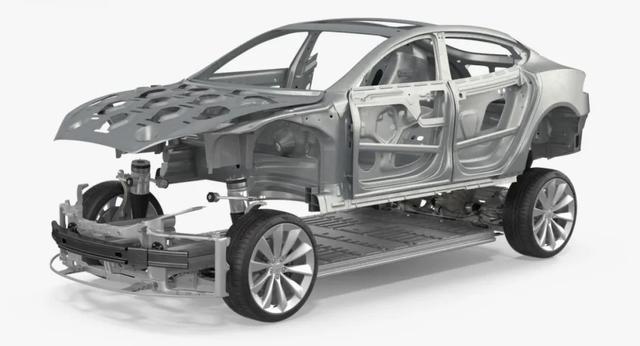
Using lightweight materials in electric vehicle (EV) construction offers several benefits, including:
- Improved energy efficiency: Lightweight materials reduce the overall weight of the vehicle, which in turn reduces the energy required to move it. This leads to increased efficiency and longer driving ranges for electric vehicles.
- Enhanced performance: Reducing the weight of the vehicle can improve its acceleration, handling, and braking performance, making it more responsive and enjoyable to drive.
- Increased payload capacity: Using lightweight materials can help increase the payload capacity of the vehicle, allowing it to carry more passengers or cargo without compromising performance or efficiency.
- Reduced wear and tear: With lower weight, there is reduced stress on various components of the vehicle, such as the suspension, brakes, and tires, resulting in lower maintenance costs and longer-lasting parts.
- Environmental benefits: Lighter vehicles require less energy to manufacture and transport, resulting in lower greenhouse gas emissions. Additionally, as lightweight materials often enable increased driving ranges for EVs, this can help reduce range anxiety and promote the adoption of electric vehicles.
- Greater design flexibility: Lightweight materials can provide more freedom for designers and engineers to create innovative and unique vehicle designs, as they can often be shaped and formed more easily than traditional materials.
Some examples of lightweight materials used in EV construction include aluminum, high-strength steel, carbon fiber, and various composite materials. The choice of materials depends on factors such as cost, manufacturing processes, and the desired performance characteristics of the vehicle.
- Improved battery performance: With a lighter vehicle, the battery pack does not have to work as hard to propel the car. This can help extend battery life and reduce the rate of degradation, leading to lower replacement costs over the long term.
- Reduced charging time: Since lighter vehicles consume less energy, charging times can be reduced, making electric vehicle ownership more convenient for users.
- Enhanced safety: Some lightweight materials, such as high-strength steel and advanced composites, possess excellent strength-to-weight ratios. By using these materials strategically in vehicle construction, it is possible to maintain or even improve safety levels while still reducing weight.
- Lower manufacturing costs: Although some lightweight materials can be more expensive upfront, the potential for reduced material usage, streamlined production processes, and lower energy consumption during manufacturing may help offset these costs in the long run.
- Material recyclability: Many lightweight materials, such as aluminum, have high recyclability rates, which can help minimize the environmental impact of vehicle production and disposal.
- Improved infrastructure compatibility: As more vehicles transition to electric power, reducing their weight can help lessen the burden on existing transportation infrastructure, such as bridges and roads, by decreasing the overall stress on these structures.
In conclusion, using lightweight materials in electric vehicle construction offers numerous benefits that can lead to improved energy efficiency, performance, and environmental sustainability. As the electric vehicle market continues to grow, advancements in lightweight material technology and production processes will likely play a crucial role in further enhancing the capabilities and appeal of electric vehicles.